An electric motor is a machine that uses the concept of conversion of energy and consequently converts electric to mechanical energy. The main parts that help propel the process are the rotor, stator, windings, air gap and commutator. The approximate efficiency of an electric motor is 70%-85% (extra energy is taken by the sound and heat emitted by it).
Whether for tasks as huge as building high rises, to ones as commonplace as warming food, electric motors play a significant role in our lives.
Uses of Electric Motors
Electric motors, both large and small, can be used in a number of ways in residential and industrial applications.
- At home, they can be used as water pumps for a number of different reasons such as central heating, fish tanks, etc. Moreover, there are a lot of electrical appliances at home that use electric motor, like food processors, DVD drives, garage door openers, power windows, etc.
- On the field, some examples of electric motors include mills, lathes, fork-lift trucks, extruders, etc. A lot of work is dependent on these machines.
How is an Electric Motor Installed?
Here are the general and specific requirements that need to be followed in order to install an electric motor
General Requirements
- The environment impacts the kind of motor that needs to be installed.
- All Variable Frequency Drive controlled motors must be rated by IEC or NEMA inverter duty.
- Article 430 of NEC must be complied with.
- If the nameplate of the motor is hidden or unclear after installation, a new one must be put up someplace where it can easily be seen.
- Special consideration has to be given to the insulation limits and if the motor is installed on a height.
- If the surface temperature exceeds 60 C, the motor needs to be provided with guarding.
- Clear signs and arrows should be propped up so that no reverse-rotation scenarios occur, causing health hazard or equipment damage.
- RTDs and a temperature relay system are necessary for motors using above 55 kW, so they shut down if very high temperatures are reached.
- There are certain performance characteristics that need to be adhered to with an S1 duty rating.
- A wire made of stranded copper must be ground insulated in the motor, with one end in the control panel that has the motor starter.
- In case of any special usage warrants or motors that require a different duty fee from those stipulated above, a P&G certified electric engineer must be notified.
- Connection of the motor through wire nuts is prohibited except for certain exceptions.
- Boxes that contain the motor junction are supposed to be made of metal.
- Continuous motor leads are expected with a ground wire running along.
- A motor must have a service factor of at least 1.15 if it is to work continuously or in an environment where the temperature exceeds 40C.
Specific Requirements
There are 3 kinds of specific requirements that you need to keep in mind:
- Global: All AC motors are to be made for 50/60 Hz and 400 VAC, and a Variable Frequency Drive is imperative for AC motors.
- U.S. Only Tools: The design of such motors must adhere to 60 Hz and 460 VAC. Moreover, those that are not controlled by VFD and with 0.75 HP or higher power rating need necessary protection for thermal overload. Those below 0.75 HP are encouraged to get overload protection.
- E.U. Only Tools: The motor designs must correspond to 50 Hz and 400 VAC. The rest of the requirements coincide with those of U.S. Only Tools.
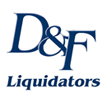
D&F Liquidators has been serving the electrical construction materials needs for more than 30 years. It is an international clearinghouse, with 180,000 square facility located in Hayward, California. It keeps an extensive inventory of electrical connectors, conduit fitting, circuit breakers, junction boxes, wire cable, safety switches etc. It procures its electrical materials supplies from top-notch companies across the globe. The Company also keeps an extensive inventory of electrical explosion proof products and modern electrical lighting solutions. As it buys materials in bulk, D&F is in a unique position to offer a competitive pricing structure. Besides, it is able to meet the most discerning demands and ship material on the same day.